Forging of α+ß titanium alloys with steel casing
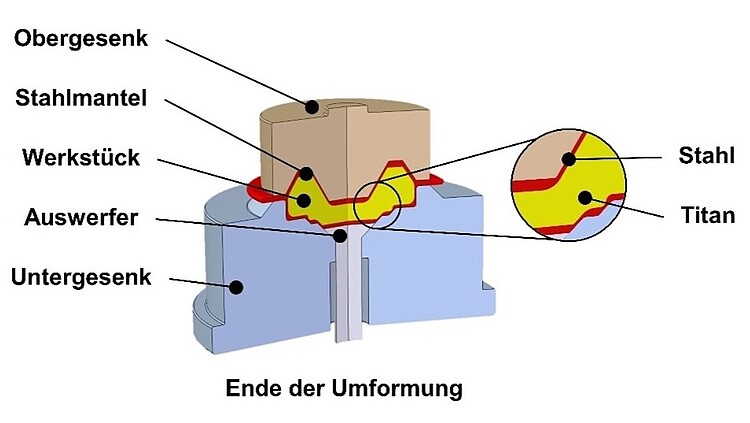
E-Mail: | massivumformung@ifum.uni-hannover.de |
Year: | 2023 |
Funding: | Deutsche Forschungsgemeinschaft (DFG) - Projektnummer 461918196 |
The aim of this project is to simplify the process of titanium die forging in order to enable a wider range of applications, for example in the production of aircraft components. The steel capsule prevents the titanium alloy from being exposed to reactive gases such as oxygen without a shielding gas atmosphere. In addition, the steel capsule acts as an insulating layer, which means that the desired temperature of the titanium alloy can be ensured during forming without the need to control the temperature of the tools. Consequently, forging can be carried out with conventional steel forging dies without using the special isothermal forging dies.
The properties of the component are strongly influenced by the process parameters during forming. The steel wall thickness used has a decisive influence on the process, as both the temperature of the internal titanium and the material flow during forming depend on it. The construction of the steel capsule is therefore carried out with the aid of numerical simulation. The encapsulation can be carried out using different methods such as shrinking or hot isostatic pressing. By varying the wall thickness, the type of encapsulation and the forming temperature, the influence of these on the material flow and the microstructure is investigated. The measurement of the forged workpieces allows the final validation of the numerical simulation. The components are then characterized by metallographic examinations and hardness tests. Based on these investigations, an optimal encapsulation strategy for the forming of titanium alloys with a low subsequent machining volume is to be determined.